Preparation of edges for welding. Form of prepared edges for welding.
Preparation of edges for welding. The elements of the geometric shape of the preparation of edges for welding (Fig. 25) include the angle of cutting the edges α, the blunting of the edges S, the length of the bevel of the sheet L in the presence of a difference in metal thicknesses, the offset of the edges relative to each other b, the gap between the joined edges a.

Rice. 25. Elements of the geometric shape of the preparation of edges for welding (a) and seam (b):
c - seam width, h - seam height, K - seam leg
The angle of cutting edges is performed with a metal thickness of more than 3 mm, since its absence (grooving) can lead to lack of fusion over the cross section of the welded joint, as well as to overheating and burnout of the metal; in the absence of cutting edges, to ensure penetration, the electric welder must increase the amount of welding current.
Edge preparation allows welding in separate layers of a small section, which improves the structure of the welded joint and reduces the occurrence of welding stresses and deformations.
The gap, correctly set before welding, makes it possible to ensure complete penetration over the joint cross section when applying the first (root) layer of the weld, if the appropriate welding mode is selected.
The length of the bevel of the sheet regulates a smooth transition from a thick welded part to a thinner one, and stress concentrators in welded structures are eliminated.
Edge blunting is performed to ensure stable conduct of the welding process when performing the root layer of the weld. The lack of blunting contributes to the formation of burns during welding.
Edge displacement creates additional welding deformations and stresses, thereby worsening the strength properties of the welded joint. Edge offset is regulated either by GOSTs or specifications. In addition, the displacement of the edges does not allow to obtain a monolithic weld over the cross section of the welded edges.
GOST 5264-80 provides for butt joints the shapes of the prepared edges shown in fig. 26; for corner joints - in fig. 27; T-shaped - in fig. 28 and overlapping - in fig. 29.
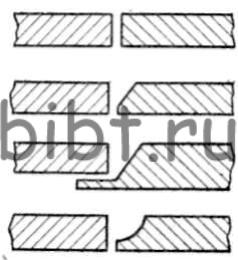
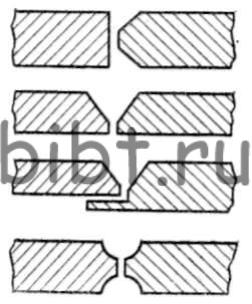
Rice. 26. Form of prepared edges for welding for butt joints
Rice. 27. Form of prepared welding edges for fillet joints

Rice. 28. Shape of prepared weld edges for tee joints
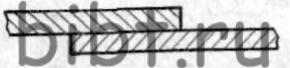
Rice. 29. Form of prepared welding edges for lap joints
The preparation of edges for welding is carried out on mechanical lathes (processing the ends of pipes), milling, planing - processing sheets, etc., as well as using thermal cutting. Sheets, pipes made of carbon steels are processed by oxy-fuel cutting. Acetylene, propane, coke oven gas, etc. can serve as combustible gases. Non-ferrous metals, as well as stainless steels, are processed by plasma cutting.
Before welding of especially critical structures, the ends of pipes or sheets after oxy-fuel cutting are additionally processed mechanically; this is done in order to avoid any inclusions in the metal.
Edge trimming is carried out on both sides with a width of at least 20 mm. When preparing the edges for welding, pay special attention to the thorough cleaning of the ends, bevels and blunts of the parts to be joined. Remember! After assembling the parts into a knot, edge preparation is useless..
The essence of preparation of cutting edges for welding A part of the metal is removed at a certain angle (bevel angle) along the joined end of the plate. Bevel edge A straight, oblique cut of an edge to be welded. Bevel angle (c) acute angle between the bevel plane and the end plane.
When removing metal from the end of the plate, it is imperative to leave a blunt. It is necessary so that during tacking and welding, quickly melting sharp edges do not create a wide gap that is difficult to weld. The lack of blunting leads to the formation of burns during welding along the butt of the welded joint.
The shape of the edge cutting is characterized by the angle of their bevel, the size of the bluntness and the gap between the welded edges. It depends on the type of welded joint (butt, corner, tee, lap, end), the thickness of the welded elements. Groove shape
For manual arc welding coated metal electrodes for metal up to 5 mm thick, as a rule, beveling of edges is not required. On elements with a thickness starting from 5 mm, as a rule, one-sided symmetrical cutting of the edges is made. The angle of cutting the edges is 6080 °.
The blunting value in all cases should be from 1 to 3 mm, depending on the thickness of the parts to be welded. with a thickness of more than 20 mm, double-sided cutting of the edges is used. In this case, the blunting ranges from 1 to 3 mm, depending on the thickness of the parts to be welded.
Ways of cutting edges for welding: Gas cutting with subsequent mechanical or manual refinement. Mechanical cutting with scissors followed by mechanical or manual finishing. Machining: for bodies of revolution, turning or carousel machining, machining on a boring machine; for rectilinear elements mechanical gouging, milling, pneumatic grinding. Manual processing: cutting with a chisel and finishing with a file.
§ 28. Preparation of metal for welding
Preparation of the metal surface for welding. When preparing parts for welding, the incoming metal is subjected to straightening, marking, basting, cutting, preparation of edges for welding, cold or hot bending.
The metal is straightened either by hand or on various straightening rollers. Manual dressing is performed on cast-iron or steel straightening plates with sledgehammer blows or using a manual screw press. Angular steel is straightened on straightening rollers (presses), I-beams and channels are straightened on driven or manual straightening presses.
Marking and basting are operations that determine the configuration of a future part. Mechanical cutting is used for straight cutting of sheets, and sometimes for curved cutting of sheets using roller shears with circular knives for this purpose. Carbon steels are cut by oxy-fuel and plasma-arc cutting. These methods can be manual and mechanized. For cutting alloy steels, non-ferrous metals, gas-flux or plasma-arc cutting can be used.
The base metal and filler material must be thoroughly cleaned of rust, oil, moisture, scale and various non-metallic contaminants before welding. The presence of these contaminants leads to the formation of welds pores, cracks, slag inclusions, which leads to a decrease in the strength and density of the welded joint.
Preparation of edges for welding. The elements of the geometric shape of the preparation of edges for welding (Fig. 25) include the angle of cutting the edges α, the blunting of the edges S, the length of the bevel of the sheet L in the presence of a difference in metal thicknesses, the offset of the edges relative to each other b, the gap between the joined edges a.
Rice. 25. Elements of the geometric shape of the preparation of edges for welding (a) and the seam (b):
c - seam width, h - seam height, K - seam leg
The angle of cutting edges is performed with a metal thickness of more than 3 mm, since this absence (cutting edges) can lead to lack of fusion over the cross section of the welded joint, as well as to overheating and burnout of the metal; in the absence of cutting edges, to ensure penetration, the electric welder must increase the amount of welding current.
Grooving allows welding in separate layers of a small section, which improves the structure of the welded joint and reduces the occurrence of welding voltage and deformations.
The gap, correctly set before welding, makes it possible to ensure complete penetration over the joint cross section when applying the first (root) layer of the weld, if the appropriate welding mode is selected.
The length of the bevel of the sheet regulates a smooth transition from a thick welded part to a thinner one, and stress concentrators in welded structures are eliminated.
Edge blunting is performed to ensure stable conduct of the welding process when performing the root layer of the weld. The lack of blunting contributes to the formation of burns during welding.
Edge displacement creates additional welding deformations and stresses, thereby worsening the strength properties of the welded joint. The offset of the edges is regulated either by GOSTs or by technical specifications. In addition, the displacement of the edges does not allow to obtain a monolithic weld over the cross section of the welded edges.
GOST 5264-80 provides for butt joints the forms of prepared edges shown in fig. 26; for corner joints - in fig. 27; T-shaped - in fig. 28 and overlapping - in fig. 29.
Rice. 26. The shape of the prepared edges for welding for butt joints
Rice. 27. The shape of the prepared edges for welding for fillet joints
Rice. 28. The shape of the prepared edges for welding for tee joints
Rice. 29. The shape of the prepared edges for welding for lap joints
The preparation of edges for welding is carried out on mechanical machines - turning (processing the ends of pipes), milling, planing - processing sheets, etc., as well as using thermal cutting. Sheets, pipes made of carbon steels are processed by oxy-fuel cutting. Acetylene, propane, coke oven gas, etc. can serve as combustible gases. Non-ferrous metals, as well as stainless steels processed by plasma cutting.
Before welding of especially critical structures, the ends of pipes or sheets after oxy-fuel cutting are additionally processed mechanically; this is done in order to avoid any inclusions in the metal.
Requirements for the assembly of metal parts before welding. The used assembly and welding fixtures must provide access to the places of installation of parts and tacks, to the handles of fixing and clamping devices, as well as to the places of welding. These fixtures must also be sufficiently strong and rigid, ensure accurate fastening of the parts in the desired position and prevent their deformation during the welding process. In addition, assembly and welding fixtures should provide the most advantageous order of assembly and welding: the least number of turns when applying tacks and welds; free access to check the dimensions of products and their easy removal after production; safety of assembly and welding operations.
Any assembly operation should not impede the implementation next operation. Parts arriving for assembly must be carefully checked; all geometric dimensions of the part and the prepared shape of the edges for welding are subject to verification.
The assembly of welded structures, as a rule, is carried out either by marking, or with the help of templates, stops, clamps or special devices - conductors that facilitate assembly operations. Preparation and assembly of products for welding is carried out in compliance with the following basic mandatory rules:
the blunting of the edges and the gaps between them must be uniform along the entire length;
the edges of the elements to be welded and the places adjacent to them with a width of 25-30 mm from the end of the edge must be dried, cleaned of burrs after cutting, oil, rust and other contaminants;
in order to avoid deformations, the tack should be performed with high-quality electrodes at intervals of not more than 500 mm with a length of one tack of 50-80 mm;
to ensure the normal and high-quality formation of the seam, it is necessary to grab the strips at the beginning and at the end of the product.
The preparation of metal for welding includes straightening, marking and basting, cutting and edge processing, cold and hot bending. Editing is carried out mainly on machines, and sometimes manually. Sheet, strip and profile products are straightened on rolls, which most often have seven or nine rolls.
The rollers are equipped with two roller tables for loading and exiting the metal during the straightening process. When straightening, the sheets are passed through the rollers 3 to 5 times.
Along with machine editing, manual editing is sometimes used. The latter is produced on cast-iron or steel straightening plates by hammer blows, sledgehammers and using a screw press.
Editing of angle steel is carried out on angle straightening rollers or on manual screw presses, and I-beams and channels on driven or manual straightening presses.
Marking and basting. In individual production, straightened metal is supplied for marking, and in mass and mass production, it is supplied for basting. Before marking and basting, the metal surface is primed with chalk paint on glue.
When marking the same type of parts for mass and serial production, metal or plywood templates are used. Marking up with templates is called basting. Hardened steel scribers, center punches, steel rulers and squares, steel compasses and thickness gauges, hammers, cleats, clamps, steel tape measures, etc. serve as tools for marking and basting.
Cutting. Metal is cut into blanks mechanically using scissors and saws or with an oxy-fuel flame. Mechanical cutting is carried out mainly with scissors and is mainly used for straight cutting of sheets up to 20 mm thick. The most widely used are guillotine shears with knives from 1 to 3 m long and press shears with knives up to 700 mm long.
For curved cuts of thicknesses up to 6 mm, roller shears with circular knives are used. For straight cuts of large thicknesses and for curved cuts of thicknesses over 6 mm, manual, semi-automatic and automatic oxy-fuel cutting is mainly used. For cold cutting of rods of round and other sections, round (circular) toothed and friction saws are used.
Edge processing for welding. Processing and beveling of edges for welding are carried out mechanically on edge-cutting and longitudinal-planing machines or with an oxy-fuel flame. With a small amount of work, cutting with a pneumatic chisel is sometimes used. Bending. Bending of sheet, strip and wide strip metal is carried out on sheet bending three-roll and four-roll rolls. Cold bending receives sheets with prepared edges and cut holes of small diameters. Profile metal bending is carried out on straightening presses and roller bending machines. The smallest permissible bending radius of steel in a cold state is recommended to be taken equal to 25 times the sheet thickness or the height of a symmetrical profile. If the radius of cold bending is less than 25 thicknesses of the wrought steel, then tears of the outer fibers are possible.
Bending of large thicknesses and bending of shells of small diameter, with an average thickness of the sheet, is carried out in a hot way in forging and pressing shops. The parts are heated to a temperature of 1000--1100°C, at which the metal can be easily deformed. Preparation of edges for welding and cutting of large holes is carried out after hot bending.
Cutting edges - giving the edges to be welded the required shape.
Cutting edges for welding is carried out in order to ensure:
Penetration over the entire thickness of the welded elements;
Access of the welding tool to the root of the seam.
According to the form of cutting edges for welding, welded joints are distinguished without cutting edges, with flanging and with cutting edges for welding. In addition, welded joints with groove edges are divided into welded joints with one-sided bevel of one or two edges (one-sided groove of one or two edges) and welded joints with two-sided bevel of one or two edges (two-sided groove of one or two edges).
When choosing the shape of the edge preparation, it should be taken into account that the most economical is a welded joint without beveled edges. In the case of cutting the edges, it is easier to perform compared to the U-shaped cutting of the edges with a straight bevel of the edges (V, K, X - shaped). In comparison with one-sided cutting of edges, K- and X-shaped double-sided ones are more technologically advanced. However, K- and X-shaped double-sided can be implemented if the welding tool can access both sides of the product.
Cutting edges for welding
MDK 02.01. Equipment, technique and technology of electric welding
PM.02. Welding and cutting of parts from various steels, non-ferrous metals and their alloys, cast irons in all spatial positions
by profession 150709.02 Welder (electric welding and gas welding).
Testing is a softer tool, they put all students on an equal footing, using a single procedure and common assessment criteria, which leads to a decrease in pre-examination nervous tension.
Download:
Preview:
budgetary educational institution Omsk region
initial vocational education
"Professional School No. 65".
TEST
Cutting edges for welding
MDK 02.01. Equipment, technique and technology of electric welding
PM.02. Welding and cutting of parts from various steels, non-ferrous metals and their alloys, cast irons in all spatial positions
By profession 150709.02 Welder (electric welding and gas welding)
Compiled by: Baranov Vladimir Ilyich master of industrial training
Sedelnikovo, Omsk region, 2013
Cutting edges for welding.
Test.
Each question has one or more correct answers. Choose the right ones.
1. Cutting edges is performed:
a) to improve welding conditions and obtain guaranteed penetration;
b) based on aesthetic considerations;
c) to prevent welding deformations.
2. Starting from what thickness on the plates, as a rule, bevelled edges are made?
a) 3 mm.
b) 5 mm.
c) 8 mm.
- The figure shows the edge:
a) with rectilinear bilateral
symmetrical bevel;
b) with a curvilinear bevel;
c) with a rectilinear one-sided bevel.
- What is a bevel angle?
a) An acute angle between the plane of the bevel of the edge and the plane of the end.
b) An acute angle between the plane of the bevel of the edge and the plane of the plate.
c) An obtuse angle between the plane of the bevel of the edge and the plane of the butt.
- The bevel angle is:
a) 45-60°;
b) 60-80°;
c) 80-100°.
6. The value of the blunting of the edges in all cases should be:
a) from 1 to 3 mm;
b) from 3 to 4 mm;
C) from 4 to 5 mm.
- On plates of what thickness is it advisable to make a double-sided bevel of the edges?
a) 10 mm.
b) 6 mm.
c) 20 mm or more.
- Metal removal using a chisel and hammer is acceptable for plate thickness starting from:
a) with 8 mm;
b) with 3 mm;
c) with 20 mm.
- In one pass, a layer of metal is removed with a chisel with a thickness of:
a) 2 mm;
b) 5 mm;
c) 4 mm.
10. When finishing the edge with a file, you must:
a) reach the edge of the core mark;
b) remove half of the core mark;
c) remove the core mark completely.
Sample response:
Test evaluation criteria:
Rating "excellent" 9-10 correct answers or 90-100% of the 10 proposed questions;
Rating "good" 7-8 correct answers or 70-89% of the 10 proposed questions;
Grade "satisfactory" 5-6 correct answers or 50-69% of 10 proposed questions;
Evaluation is unsatisfactory» 0-4 correct answers or 0-49% of 10 proposed questions.
List of used literature
- Galushkina V.N. Technology of production of welded structures: a textbook for the beginning. prof. education. - M.: Publishing Center "Academy", 2012;
- Ovchinnikov V.V. Technology of manual arc and plasma welding and cutting of metals: a textbook for the beginning. prof. education. - M.: Publishing Center "Academy", 2010;
- Maslov V.I. Welding works6 Proc. for the beginning prof. education - M .: Publishing Center "Academy", 2009;
- Ovchinnikov V.V. Equipment, technique and technology of welding and cutting of metals: textbook - M.: KNORUS, 2010;
- Kulikov O.N. Occupational safety in the production of welding works: textbook. allowance for the beginning prof. education - M .: Publishing Center "Academy", 2006;
- Vinogradov V.S. Electric arc welding: a textbook for the beginning. prof. Education - M .: Publishing Center "Academy", 2010.