Gas pipelines are built to transport natural gas to consumers. They are designed by design organizations that have received a license to carry out such work. For the installation of gas pipelines, pipes from various steel grades are used in various ways (at different temperatures and pressures). According to the production method, steel pipes for gas can be divided into seamless (hot-formed and cold-formed) and welded (with a straight and spiral seam).
Steel for the production of products of this type must comply with GOST 380 88. Specifications are regulated by GOST 1050 88. The thickness of the pipes is determined using calculations, given that for an underground pipeline it must be at least 3 mm, for ground pipelines - at least 2 -x mm. The gas pipe must be certified. The documents must indicate the manufacturer, GOST, steel grade, production method, test information, batch number, quality control mark of conformity.
Scopes of steel pipes for gas pipelines:
- - in gas supply systems with pressure up to 1.6 MPa - water and gas pipes (GOST 3262-75) with nominal bore up to 80 mm;
- - in gas pipelines with different pressure - seamless steel pipes (GOST 8734-75 and GOST 8732-78), withstanding pressure up to 10 MPa;
- - in gas pipelines with high pressure - welded longitudinal pipes (GOST 10704-76) with a diameter of 30 to 426 mm and a wall thickness of 3 to 12 mm.
Advantages of steel pipes for gas
Steel pipes for gas pipelines:
- - durable;
- - resistant to internal pressure;
- - linear expansion of steel pipes is 20 times less than that of polyethylene pipes;
- - 100% gas tightness, which eliminates gas leaks.

Disadvantages of steel pipes for gas:
- - tendency to corrosion, leading to a decrease in the internal cavity;
- - relatively large weight;
- - labor-intensive and time-consuming installation;
- - high thermal conductivity, leading to the formation of condensate on the outer surface, as a result of which the corrosion process begins;
- - welded joint - the most vulnerable to rust;
- - restrictions in the length of the supplied products;
- - limited flexibility.
Gas pipeline installation
Pipeline requirements:
- - the position must be fully consistent with the project;
- - on the gas pipeline, the insulation, which is equipped with steel gas pipes, must be completely preserved;
- - all connections must be 100% tight, not leaking;
- - pipes must fit snugly to the base;
- - the bed should be kept;
- - Mandatory elements are water traps (to drain condensate from the outer surface) and compensators (to neutralize the linear expansion of the pipe).
A trench for a gas pipeline cannot be prepared in advance. Its bottom must be cleared of debris and stones. The gas pipeline is assembled from separate elements that are welded outside the trench. When lowering individual elements into the trench, impacts against the walls or bottom are not allowed. If the gas pipeline is laid in winter, then the trench must be dug to the unfrozen ground immediately before laying the elements. On rocky soils, a sand bed (approx. 200 mm) is required.
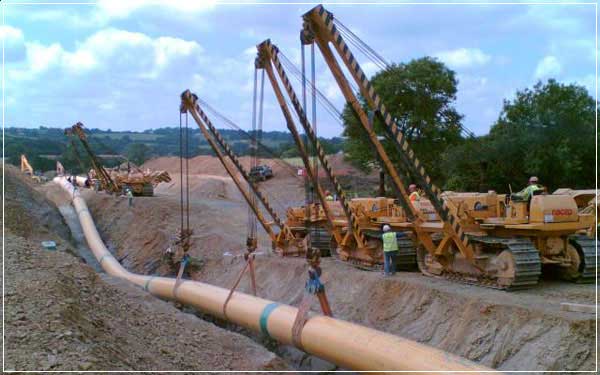
Insulation of the outer surface of steel pipes
If the pipeline is laid in the ground, it is exposed to corrosion and stray currents that destroy its walls. To prolong the service life of the pipes, they are coated with various anti-corrosion insulating materials at the factory. During transportation and installation, the pipes should be handled with care, since it is quite difficult to restore the insulation in the field.

During installation, work is still required to isolate the seams, which are formed after welding of individual elements of the pipeline. For this purpose, various anti-corrosion coatings based on bitumen and roll materials (kraft paper or polymer) are used. Depending on the properties of the soil, anti-corrosion insulation can be normal, reinforced or very reinforced.
The pipe is cleaned to a metallic sheen. Then a primer is applied to it. Bituminous mastic is prepared in bituminous boilers and applied to the primer with a watering can while it is hot. A rolled insulating material is wound over the mastic with an overlap.
Internal insulation of steel pipes
Epoxy materials are most often used for internal insulation of steel pipes. They prevent corrosion of the inner surface and the formation of other deposits, keeping the flow rate unchanged.
The pipeline for transporting gas consists not only of steel pipes, but also of valves, hydraulic gates, compensators and condensate collectors. Cranes are made of cast iron, steel and bronze with a diameter of 15 - 700 mm. The gates act as shut-off devices - to turn off the gas, water is supplied to the pipeline, which fills the lower part of the gate, interrupting the flow of gas. To reconnect the gas, the water is removed by blowing. Valves are tested for durability at the factory.
Compensators are mounted in wells and connected to the gas pipeline. At sub-zero temperatures, they are stretched before installation, at positive temperatures, they are compressed. Condensate collectors collect condensate from the gas pipeline, therefore they are mounted at its lower points. Periodically, water from these devices must be removed.
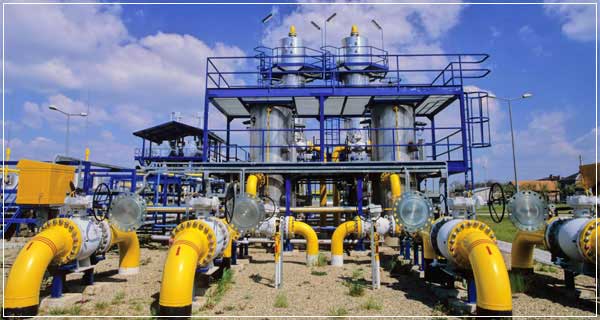